由单相或三相电网电源或储能系统(ESS) 供电的直流母线电压为 400 V 或更高的电气系统可以通过固态电路保护来增强其可靠性和弹性。设计高压固态电池断路开关时,需要考虑几个基本设计决策。其中关键因素包括半导体技术、器件类型、热封装、器件耐用性以及电路中断期间的感应能量管理。本文讨论了选择功率半导体技术和定义高电压、大电流电池断路开关的半导体封装时的设计注意事项,以及表征系统寄生电感和过流保护限制的重要性。
宽禁带半导体技术的优势
需要仔细考虑选择的半导体材料,以实现具有导通电阻、截止状态漏电流、高电压阻断能力和高功率能力的开关。图 1 显示了硅 (Si)、碳化硅 (SiC) 和氮化镓 (GaN) 的半导体材料特性。 SiC和GaN的电击穿场大约是硅的十倍。这使得能够设计漂移区厚度为等效额定硅器件十分之一的器件,因为其厚度与电击穿场成反比。而且,漂移区的电阻与击穿场的三次方成反比。这导致漂移区电阻降低近 1000 倍。在固态开关应用中,所有损耗都是传导损耗,高击穿场是一个显着的优势。这种降低的电阻还消除了对动态闩锁问题的担忧,其中高 dV/dt 瞬态可能分别触发硅功率 MOSFET 和 IGBT 中的寄生 NPN 晶体管或晶闸管。
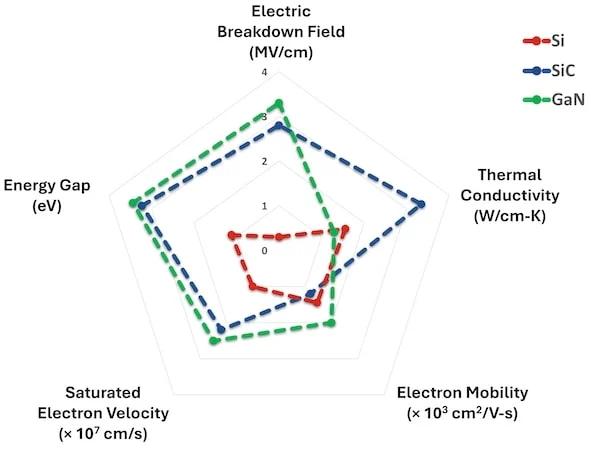
图 1.Si 、SiC 和 GaN 材料特性。图片由博多电力系统提供
碳化硅的导热率是硅和氮化镓的三倍,显着提高了芯片的散热能力,使其运行温度更低并简化了热设计。或者,对于等效的目标结温,它允许更高的电流运行。较高的导热率与高击穿场相结合,导致导通电阻较低,进一步简化了热设计。
碳化硅是一种宽带隙(WBG)半导体材料,其能隙接近硅的三倍,可以在更高的温度下工作。半导体在高温下不再发挥半导体的作用。由于自由电荷载流子的浓度较低,更宽的能隙使得碳化硅的工作温度比硅高数百摄氏度。然而,基于当今技术的其他因素(例如封装、栅极氧化泄漏)将器件的连续结温限制为 175°C。 WBG 技术的另一个优点是它提供较低的断态漏电流。
考虑到这些特性,碳化硅是该应用的半导体材料。
IGBT、MOSFET 和 JFET 之间的差异
晶体管的类型是下一个关键因素。在大多数情况下,传导损耗是的设计挑战。应尽量减少传导损耗以满足系统的热要求。某些系统可以使用液体冷却,而其他系统则可能使用强制通风或依靠自然对流。除了的传导损耗之外,还必须将压降保持在限度,以限度地提高所有工作点(包括轻负载条件)的效率。这对于电池供电的系统尤其重要。许多系统(包括直流系统)中的另一个重要因素是双向电流。通常需要具有低传导损耗、低电压降和反向导通能力的晶体管。通常考虑的晶体管有 IGBT、MOSFET 和 JFET。
虽然 IGBT 在峰值负载电流下提供与 MOSFET 相当的传导损耗,但一旦负载电流降低,基于 IGBT 的解决方案的效率就会降低。这是因为电压降由两个部分组成:独立于集电极电流的近乎恒定的电压降和与集电极电流成比例的电压降。对于 MOSFET,压降与源电流成正比。它没有 IGBT 的开销,因此可以在所有工作点(包括轻负载条件下)实现高效率。 MOSFET 允许和第三象限的沟道导通,这意味着电流可以正向和反向流过器件。 MOSFET 第三象限操作的另一个好处是它的通态电阻通常比象限稍低。而IGBT只在象限导通电流,需要反并联二极管来导通反向电流。 JFET 是一种较旧的技术,但正在复兴,它可以正向传导和反向传导,并且与 MOSFET 一样,具有与漏极电流成比例的压降。它与 MOSFET 的不同之处在于它是耗尽型器件。也就是说,JFET 常开且需要栅极偏压来抑制电流流动。这给设计人员在考虑系统故障情况时带来了实际挑战。作为一种解决方法,可以使用包含一系列低压硅 MOSFET 的级联配置来实现常关器件。添加串联硅器件会增加复杂性,从而削弱 JFET 在高电流应用中的一些优势。 SiC MOSFET 是一种常关器件,可提供许多系统所需的低电阻和可控性。
热包装
SiC 电源模块可实现高水平的系统优化,而这是通过并联分立 MOSFET 难以实现的。 Microchip 的 mSiC 模块有多种配置以及电压和电流额定值。其中包括共源配置,它以反串联配置连接两个 SiC MOSFET,以实现双向电压和电流阻断。每个MOSFET由多个芯片并联组成,以实现额定电流和低通态电阻。对于单向电池断路开关,两个 MOSFET 并联连接到电源模块外部。
需要低通态电阻和低热阻来保持芯片冷却运行。模块内使用的材料是决定从结到外壳的热阻及其可靠性的重要元素。具体来说,芯片粘接、基板和底板材料特性是模块热阻的主要影响因素。选择具有高导热率的材料有助于限度地降低热阻和结温。除了热性能之外,选择热膨胀系数 (CTE) 紧密匹配的材料还可以通过减少材料界面和内部的热应力来延长模块的使用寿命。表 1 总结了这些热特性。氮化铝 (AlN) 基板和铜 (Cu) 基板是 mSiC
功率模块的标准配置。氮化硅 (Si 3 N 4 ) 基板和碳化硅铝 (AlSiC) 基板的选项可提供更高的可靠性。图 2 是采用标准 SP3F 和 SP6C 封装以及符合 DO-160 标准的高可靠性无基板 BL1 和 BL3 封装的共源电源模块。
器件坚固性和系统电感
除了模块的热性能和长期可靠性之外,电路中断装置的另一个设计考虑因素是高感应能量。继电器和接触器的循环次数有限。它们通常具有空载机械开关周期和显着减少的电负载开关周期。系统中的电感会导致触点上产生电弧,从而在电流中断时导致性能下降。因此,电气循环额定值的工作条件是明确定义的,并且对其寿命有很大影响。即便如此,在带有接触器或继电器的系统中仍需要上游熔断器,因为在承受高短路电流时触点可能会被焊断。固态电池断路开关不会受到这种退化的影响,从而实现更高可靠性的系统。尽管如此,了解系统的寄生和负载电感和电容对于管理中断高电流时存在的感应能量也至关重要。
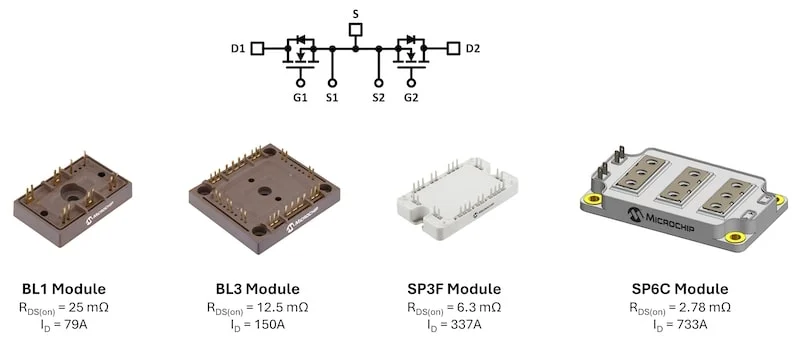
图 2. 采用共源配置的 Microchip mSiC 模块。图片由博多电力系统提供 [PDF]
感应能量与电感以及中断时系统电流的平方成正比。开关输出端的短路会导致电流快速增加,其上升速率为电池电压与源电感之比。例如,800 V 总线电压和 5 微亨源电感会导致电流以每微秒 160 A 的速率增加。检测和响应的响应时间为 5 微秒,将在电路中产生 800 A 的额外电流。由于不建议在雪崩模式下运行 SiC 功率模块,因此需要缓冲器或钳位电路通过吸收这种感应能量来保护模块。然而,当正确设计以满足爬电距离和间隙要求时,缓冲电路中引入的寄生效应会进一步限制其有效性。因此,开关关断的速度应足够慢,以限制模块内部电感造成的电压过大以及电流的突然下降。采用低电感设计的模块有助于进一步化这种电压应力。
在硅功率器件中,高电流的快速中断会带来触发寄生 NPN 或晶闸管的风险,从而导致无法控制的闩锁和终故障。在 SiC 器件上,非常快的关断可能会导致每个芯片在关断时发生低能量雪崩击穿,直到??缓冲器或钳位器吸收高能量。 Microchip 的 mSiC MOSFET 专为非钳位电感开关 (UIS) 耐用性而设计和测试,可在缓冲器或钳位开始退化时提供额外的安全裕度。显示了与市场上其他 SiC 器件相比的单次和重复 UIS 性能。
虽然应该了解器件级短路能力,并且 IGBT 确实比 MOSFET 具有更优越的器件级短路性能,但在实际系统中它会受到不同的应力条件。由于系统电感固有的限流行为,模块不太可能达到其短路电流额定值。限制因素是缓冲器或钳位电路设计。为了设计经济高效且紧凑的缓冲器,允许的系统级峰值短路电流将被限制为远低于模块的短路电流额定值的值。例如,在由九个并行芯片组成的 500 A 电池断路开关中,设计用于防止短路电流超过 1350 A,假设电流分布均匀,每个芯片传导的电流为 150 A。该电流比设备级短路测试中的电流低得多,在设备级短路测试中,测试期间电流超过数百安培。电压钳位器件的优化是鲁棒固态电池断路开关设计的关键部分。