新能源汽车充电焦虑难题,一直在行业内备受关注。下一代汽车制造商已完成从400V向800V乃至更高的技术架构迈进。然而,电池内能量密度的“跃进”,让随之而来的电池热失控问题,再一次走向舆论的风口浪尖。
值得注意的是,大功率快充的实现对于新能源汽车产业链而言”牵一发而动全身”,电池材料、电池结构、模组设计等领域,亟需不断突破技术瓶颈。艾利丹尼森作为全球材料领域的先驱者,持续深耕新能源电池材料领域多年。近期,艾利丹尼森重磅推出新能源电池绝缘膜材料解决方案,致力于破解电池热失控难题,助力新能源汽车领域主机厂、电池厂等上下游企业,既能乘风而起,也能安全落地。
电池绝缘膜应用场景
通常,电池绝缘膜产品的应用场景有三种:电池模组的端板及侧板绝缘①,例如355模组,390模组及590模组等;电池包箱体绝缘,目前,越来越多的厂家采用电池无模组(CTP)设计。CTP设计,通过将集成电池成组方式中的模组环节取消,并直接将电芯集成在电池包内。这一技术创新,对电池包箱体内②的绝缘性能及其他零部件例如液冷板③等提出更高要求。绝缘的实现通常采用喷粉和覆膜两种方案,主流的覆膜工艺包括:室温贴膜、热压、UV光照等。
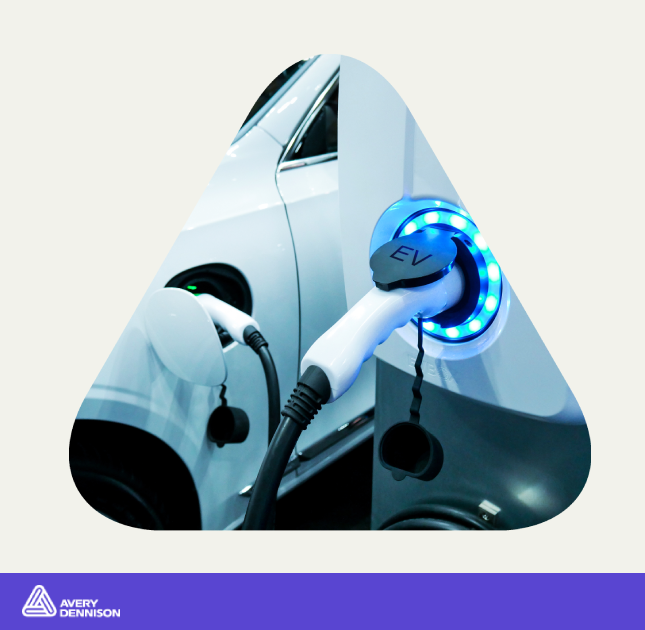
电池绝缘膜的性能要求
随着快充等创新技术的持续落地,新能源汽车上下游企业随之对电池绝缘膜的性能提出诸多要求。主要包括:耐电压强度、耐高温、阻燃、粘接强度、可靠性和作业性七大领域。
耐电压强度:绝缘膜材料耐电压强度的常见要求为3.7千伏交流或4.2千伏直流。但部分项目尤其海外地区,需要绝缘膜材料耐电压强度高达5千伏甚至10千伏,同时要求即使在高温高湿条件下,材料也需要具备绝缘性能。
耐高温:制作绝缘膜的有机高分子材料,耐受温度通常不会超过400℃,然而在电池热失控情况下,电池温度通常高达800乃至1200℃,此类情况对绝缘膜材料的耐高温性能提出巨大挑战。
阻燃:电动汽车起火乃至爆炸,一直是消费者、电池厂商和整车厂的心头大患,越来越多的行业参与者开始愈发关注材料的阻燃性能。
粘接强度:车辆在运行过程中会产生持续震动,震动对薄膜材料的耐剪切性能及可靠粘接性能提出较高要求。
可靠性:不同于手机、电脑等生命周期较短的消费电子终端,作为新一代智能电子终端的新能源汽车,产品生命周期通常高达8-10年。“超长待机”对材料的抗老化和可靠性带来挑战。
作业性:液冷板及箱体内部实现绝缘,需要粘贴较大面积的绝缘膜材料。粘贴过程中若出现气泡或皱纹,会导致材料浪费,并对生产节奏带来不利影响,最终影响产品上市周期。
艾利丹尼森绝缘膜材料解决方案,通过持续性的技术创新,助力新能源汽车上下游企业逐鹿高增量市场,有效应对材料绝缘性挑战。
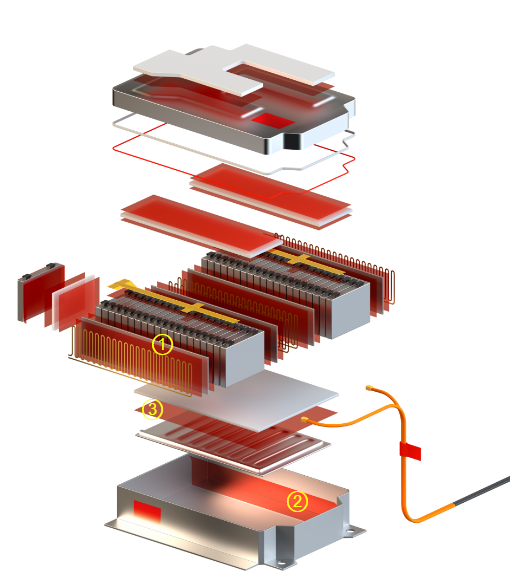
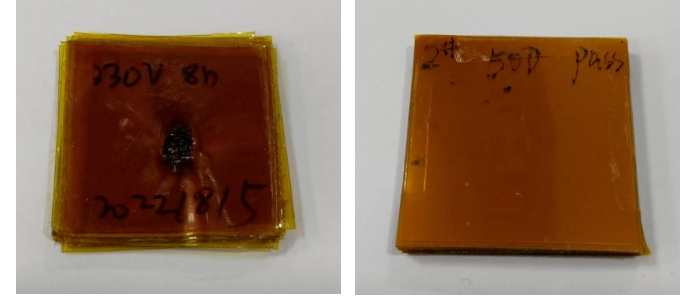
一般PI产品 CTI 600处理产品
针对耐高温难题,艾利丹尼森的特殊涂层,能够使PI材料高温耐受性能得到显著提升。通常可耐受500℃,部分型号可耐受高达800℃高温。
面对阻燃难题,艾利丹尼森研发出达到UL VTM-0标准的特殊涂层和胶水,全面覆盖覆盖经济型、常规型与优质型解决方案。值得一提的是,阻燃涂层不仅满足阻燃要求,也能耐受双倍于国家标准的1000小时的老化测试,为汽车“超长待机”保驾护航。
针对粘接强度,艾利丹尼森拥有不同种类的胶水解决方案。例如:可达2兆帕以上剪切强度的压敏胶水,可达7兆帕以上剪切强度的热激活胶水以及5兆帕以上剪切强度的UV光照胶水。
与此同时,通过特殊处理,艾利丹尼森成功提升胶水的润湿效果与排气效果,即使在钣金件等高难度表面,也可实现无气泡粘接,保证工艺的可操作性和外观效果。
免责声明: 凡注明来源本网的所有作品,均为本网合法拥有版权或有权使用的作品,欢迎转载,注明出处。非本网作品均来自互联网,转载目的在于传递更多信息,并不代表本网赞同其观点和对其真实性负责。