逆变器是将直流电压转换为交流电压的任何光伏系统的关键组件。其效率很大程度上受到功率
晶体管的开关损耗的影响。
通过正确的电路拓扑以及的元件选择可以实现的效率。为了提高效率,由带隙更宽的半导体材料制成的GaN或SiC晶体管越来越多地应用于逆变器中。然而,此类技术的成本明显高于硅基元件。
因此,具有成本效益的系统需要创新的电路设计,该设计应实现尽可能高的效率,同时使用硅基元件。 使用半桥,我们将解释如何通过显着降低开关损耗来优化逆变器的效率。作为示例,我们考虑了从阻塞上开关晶体管的续流
二极管到下开关晶体管的电流换向(图 1)。
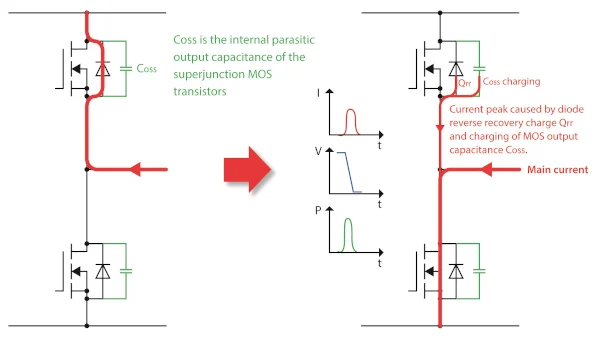
切换半桥时的电流换向和功率损耗机制
图 1:切换半桥时的电流换向和功率损耗机制
与电阻损耗一起发生的开关损耗由两种功率损耗机制决定。一是存储在续流二极管中的反向恢复电荷(Q rr )。这导致激活的下部开关晶体管中出现电流峰值,该晶体管转变为导通状态。另一种是上开关晶体管的 输出电容(C OSS )反转期间出现的充电电流峰值。
图 2 中所示的两种开关拓扑 – 同步反向阻断 (SRB) 和 SRB 1 (A-SRB) – 大大减少了开关损耗的来源。
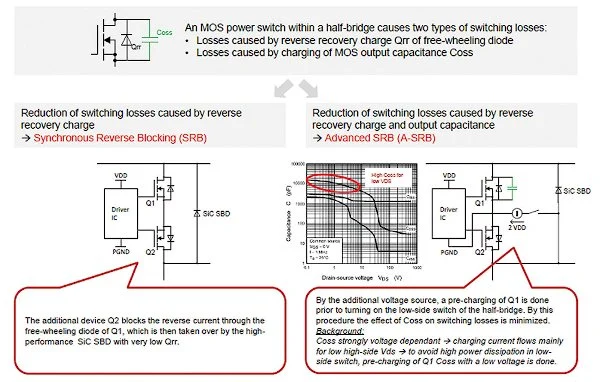
图 2:降低半桥开关损耗的技术
通过同步反向阻断(SRB),开关晶体管Q1的续流二极管中的反向电流被串联连接的第二开关晶体管Q2阻断。 Q2 与 Q1 同步控制。反向电流通过具有高击穿电压和极低反向恢复电荷的并联碳化硅 (SiC)
肖特基二极管。这显着降低了 Qrr 的影响。 Q2 的续流二极管已极化,因此该晶体管上不会形成高电压。低压型(60V)就足够了。
借助 SRB (A-SRB),通过将 Q1 预充电至低电压,可显着降低重新加载 Q1 输出电容时造成的功率损耗。漏极-源极电压VDS上的输出电容C OSS的特性表现出非常高的电压依赖性。 VDS 从 0 增加到大约 40V 会使电容减小 100 倍。这意味着在开关过程中,当 Q1 的 VDS 较低时,主要会出现导致损耗的充电电流。然而,Q1 上的低电压与转换到导通状态的半桥下部晶体管上的高电压同样重要。因此,充电电流峰值会产生高功率损耗。 在半桥下开关晶体管导通之前,C OSS由 Q1 预充电至 40V,意味着充电电流的主要部分不流过该晶体管,因此几乎不会造成功率损耗。预充电由附加电压源执行,该电压源通过栅极驱动器 IC 中的电荷泵实现。
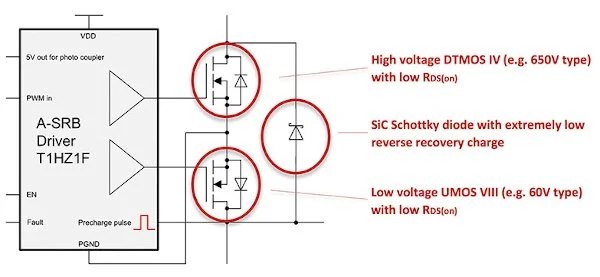
A-SRB 电路拓扑的组件
图 3:A-SRB 电路拓扑的组件 图 3 显示了 A-SRB 电路拓扑的关键组件。实际的开关晶体管(Q1)是高压超结DTMOS IV型MOSFET,其阻断电压例如为650V。与Q1串联的辅助晶体管Q2是低压超结UMOS VIII型MOSFET,阻断电压为60V。续流二极管采用反向恢复电荷极低的 SiC 肖特基二极管。这种特殊的电路拓扑由专用的T1HZ1F驱动器IC控制。该 IC 根据 PWM 输入信号生成晶体管栅极所需的所有控制信号以及用于对 Q1 输出电容进行预充电的充电脉冲。
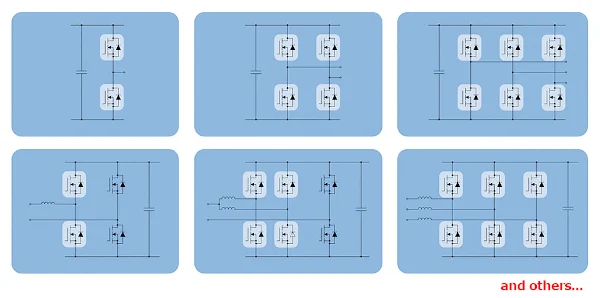
适用于 A-SRB 的电路拓扑
图 4:适合 A-SRB 的电路拓扑
东芝的 A-SRB 技术可大大降低开关损耗。它适用于广泛的应用,例如
太阳能逆变器、DC/DC 转换器、功率因数校正 (PFC) 和电机驱动控制。图 4 显示了适合 A-SRB 的电源转换器拓扑选择。突出显示的晶体管只需替换为图 3 中所示的 A-SRB 电路拓扑。 使用 A-SRB 提高效率 为了证明 A-SRB 的有效性,在使用和不使用 ASRB 的情况下对逆变桥(H4 拓扑)进行了 SPICE 仿真。对于双极性调制,图 5 显示了使用具有低 RDS(on)(100A、600V)的东芝 DTMOS IV 型开关晶体管时,A-SRB 在不同输出功率和开关频率下实现的更高效率。由于 A-SRB 降低了开关损耗,因此可以在高开关频率下实现效率增益。本例中实现的效率增益约为 4%。
该系统的主要部分,具有 A-SRB 功能的逆变桥,可以根据额定功率以不同的方式实现。对于输入功率约为300W的模块逆变器,东芝提供T1JM4模块。它集成了一个完整的半桥,包括具有 A-SRB 功能的栅极驱动器、开关晶体管和 SiC 肖特基二极管。对于输入功率高达 5kW 的太阳能逆变器,分立式栅极驱动器可作为与
开关元件组合的套件提供。
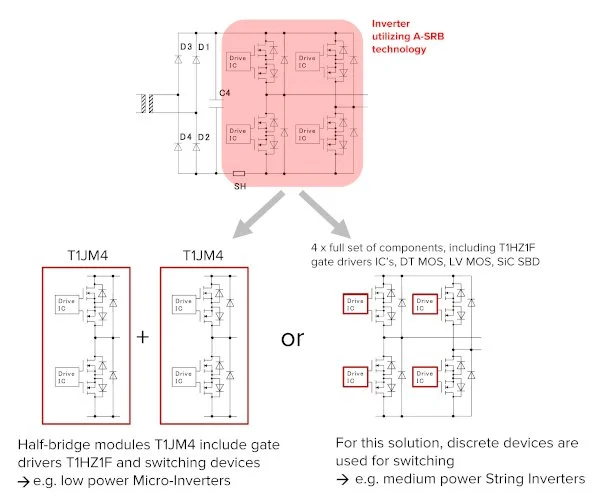
图 6:使用 A-SRB 实现逆变桥的不同选项