电动汽车(EV) 车队的快速增长推动了对充电基础设施的强劲需求,以延长电动汽车的行驶里程。直流快速充电站可以将充电时间从几小时缩短到几分钟。在设计直流快速充电站时,关键问题之一是电气安全,可以通过使用
光耦合器来解决。
电网以交流电形式传输电力,而车载电池中存储的能量为直流电,因此需要充电器来完成转换工作。根据充电机是否安装在车内,充电机可分为车载充电机(OBC)和非车载充电站。 OBC 接受市电的交流电源,然后转换为直流电来给电池充电,但由于充电器的额定功率有限,充电速度很慢。直流充电通常用于非车载充电站。它直接向车内的电池提供稳压直流电源。由于直流充电设备安装位置固定,体积限制不大,其额定功率可达数百千瓦。直流快速充电方法将充电时间从几小时缩短到几分钟[1]、[2]。图 1 说明了交流和直流充电方法。直流快速充电是成功推出电动汽车以减少或消除里程焦虑的关键工具。

图 1:交流充电和直流充电
设计具有安全隔离功能的充电站
直流快速充电站通常包括交流到直流整流器、功率因数校正 (PFC) 级、直流到直流转换等功能块,以调节适合车辆电池充电的电压水平。能量传输和充电器与车辆之间的通信是通过充电器耦合器接口完成的。图 2 显示了直流充电站设计的简化框图。在该图中,功能块中设计了一个安全隔离屏障。这对于确保设计安全符合监管标准非常重要。
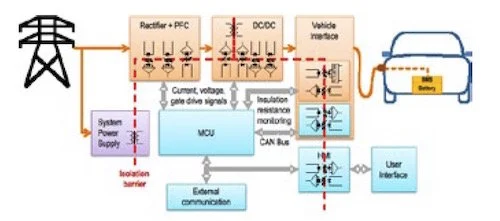
电动汽车充电站的框图。
图 2:电动汽车充电站的框图。
在 PFC 级中使用光耦合器
功率因数校正 (PFC) 级是将输入电流转换为接近与电网电压同相的正弦波形。这是为了减少注入电网的谐波,提高功率因数,以符合各种标准。 PFC 级还生成稳定的直流输出电压,为下游 DC-DC 转换器供电。图 3 显示了交错式 PFC 级的示例。
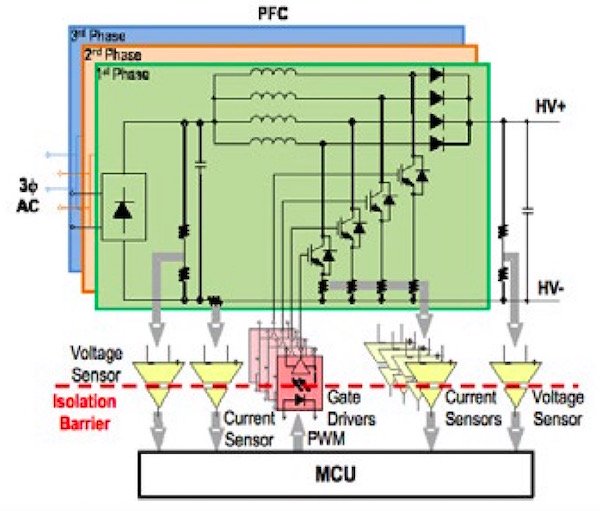
在 PFC 级中使用栅极驱动、电流和电压检测光耦合器。
图 3:在 PFC 级中使用栅极驱动、电流和电压检测光耦合器。
在此阶段,MCU(微控制器单元)根据控制算法改变 PWM(脉宽调制)信号来开关功率 MOSFET 或 IGBT 以及每个状态的持续时间。栅极驱动器用于放大具有较大电压和电流幅度的 PWM 信号,以便以所需频率驱动功率开关器件。
图 4 显示了栅极驱动电路示例。在此电路中,ACPLW349 具有 2.5 安培输出电流、轨到轨输出电压范围、55 ns 极短的传播延迟时间。该器件采用 SSO-6 小型表面贴装器件封装,根据 UL1577 标准,隔离电压额定值为 5000 Vrms,持续 1 分钟;根据 IEC/EN/DIN EN 60747-5-5 标准,隔离电压额定值为 1140 Vpeak。这些标准确保了控制器和用户侧的安全。
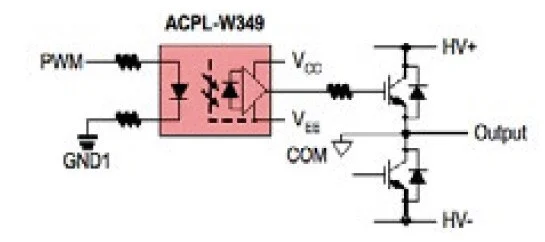
简化的栅极驱动光耦合器应用电路。
图 4:简化的栅极驱动光耦合器应用电路。
在PFC阶段,需要各种电压和电流信号来实现控制算法。这些包括整流输入电压、每个交错相的电流、总电流和直流母线电容器电压。
测量高电压的典型方法是使用电阻分压器将电压降压至适合线性传感芯片测量并发送至 MCU 的水平。电流检测电路通常采用精密分流电阻将电流转换为小电压,然后通过一些信号调理器件发送至 MCU。为了将信号从 PFC 和 DC-DC 转换器级等高压区域准确传输到低压 MCU 侧,ACPL-C87X 系列和 ACPL-C79X 系列等
隔离放大器可以方便地执行电压和电流感测函数[4]、[5]。
使用 ACPL-C87X 隔离电压传感器非常简单,如图 5 所示。假设 ACPL-C87X 的 VIN 标称输入电压为 2 V,则根据 R1 = (VL1-VIN)/ VIN×R2 选择电阻器 R1。缩小后的输入电压经过由 R2 和 C1 组成的抗混叠滤波器进行滤波,然后由 ACPL-C87X 进行检测。隔离差分输出电压(VOUT+-VOUT-)通过后置放大器U2转换为单端信号VOUT。 VOUT 与高压侧的线电压成线性比例,可以安全地连接到系统微控制器。当 ACPL-C87X 的典型增益为 1 时,整体传递函数就是 VOUT = VL1/ (R1R2+1) [4]。
高压测量并转换为隔离接地参考输出。
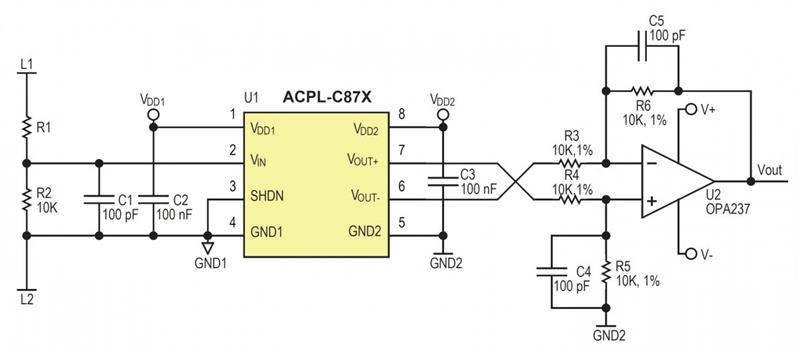
图 5:高压测量并转换为隔离接地参考输出。
使用隔离放大器来感测电流非常简单,只需将分流电阻器连接到输入并通过隔离栅获得差分输出即可,如图 6 所示。通过选择适当的分流电阻器,可以实现宽范围的电流,从较小的电流到大于1A至大于100A均可测量。在操作中,电流流过分流电阻器,ACPL-C79X 感测由此产生的模拟电压降。在光隔离栅的另一侧产生差分输出电压。该差分输出电压与电流幅度成正比,并且可以使用运算放大器(如图 5 中所示的后置放大器)转换为单端信号,或发送到控制器的模数转换器 (ADC)直接[5]。
典型的电流检测应用电路。

图 6:典型电流检测应用电路。
在 DC/DC 转换器中使用光耦合器
如图 7 所示,PFC 级之后是 DC/DC 转换器级,提供稳定的直流能量并直接传输至电池。需要测量输出电压和电流并反馈给MCU进行计算,从而调整PWM信号。然后,这些 PWM 信号将控制栅极驱动光耦合器来驱动 IGBT 或 MOSFET。在此阶段,应沿着电源变压器和栅极驱动器、电压和电流检测光耦合器观察电流隔离屏障。请参阅图 4、图 5 和图 6 了解栅极驱动、电压检测和电流检测电路。
简化的 DC/DC 转换器。
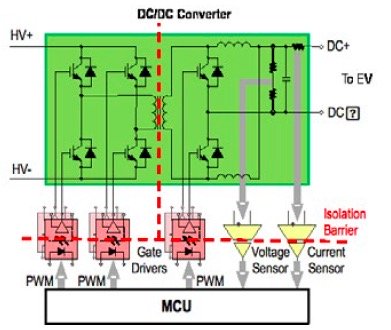
图 7:简化的 DC/DC 转换器。
在充电车接口中使用光耦合器
先进的控制方案对于实现充电站和电动汽车之间的充电控制协议是必要的。的插头标准CHAdeMO(基于快速充电类型的电动汽车销售)[6]选择CAN(控制器局域网)进行快速充电,认可其高通信可靠性。 CHAdeMO标准提供了一对在耦合器接口处连接充电器侧和车辆侧的CAN总线。耦合器引脚 8 和 9 被分配为 CAN-H 和 CAN-L,[7,第 7 页]。分别是可连接 CAN 收发器的“技术细节”。在 CAN 收发器和 CAN 控制器之间添加光隔离可显着提高系统安全性,因为光耦合器提供了安全屏障,可防止级联对系统 MCU 造成任何损坏。这种布置还可以在极其嘈杂的环境(例如高压电池充电系统)中实现更可靠的数据通信。图 8 显示了如何使用光耦合器为快速充电站设计实现隔离式 CAN 总线数字通信。类似的电路适用于需要汽车级部件的车辆侧。

隔离 CAN 总线数字通信。
图 8:隔离式 CAN 总线数字通信。
在图 8 所示的示例电路中,一对 10 MBd 快速光耦合器 ACPL-W61L 用于数据发送和接收。该产品需要 1.6 mA 极低的 LED 电流才能工作,并采用 SSO-6 封装,尺寸不到传统 DIP-8 封装的一半。尽管采用小型封装,ACPL-W61L 根据 UL1577 等级,可承受 5000 Vrms 的高压 1 分钟。
绝缘电阻监测电路的示例。
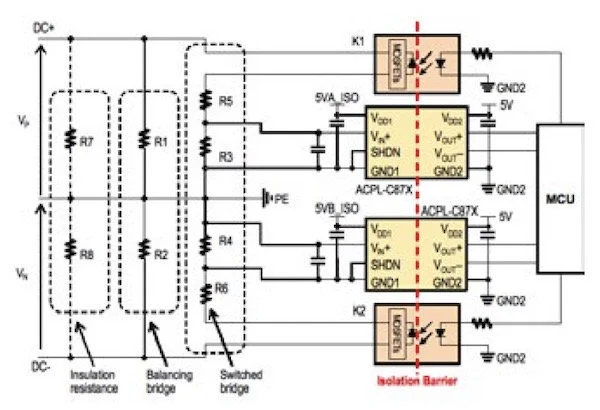
图 9:绝缘电阻监测电路示例。
该器件设计用于在存在强瞬态噪声的情况下传输信号,可保证 35 kV/μs 的共模瞬态抗扰度 [8]。如果设计需要不同,也可以使用其他光耦合器代替ACPL-W61L。其中包括 5 MBd 额定 ACPL-W21L [9] 和 25 MBb 双通道双向 ACSL7210 [10]。
作为安全措施之一,需要在电动汽车充电站中包含绝缘电阻监测功能[11]。图 9 显示了一种可能的实现方式。在该电路中,隔离放大器 ACPL-C87X 测量其输入端的电压信号,并将输出发送到 MCU。 ASSR-601J 由一个 LED 输入侧和两个位于输出侧的分立高压 MOSFET 组成。在应用中,MOSFET的两个源极节点可以作为开关的两个接
触点。在关闭模式下,它们可以承受 1500 V 以上的击穿电压。 ACPL-C87X 和 ASSR-601J 均采用光耦合技术来提供电流隔离,同时穿过隔离栅发送信号,该技术已通过 IEC 60747-5-5 ,工作电压为 1414Vpk [12]。