在电源转换器中,输入电容器通过感应电缆馈送到电源。首次插入系统时,寄生电感将导致输入电压的振铃几乎达到其直流值的两倍(也称为热插拔)。电源转换器输入阻尼不足和缺乏浪涌控制可能会损坏转换器。 使用输入大容量电解电容器来抑制非电池转换器的输入电压,可以防止首次使用电池电源时出现过多的电压振铃,同时还可以防止可能导致转换器不稳定的谐振。随着传统 12 V 汽车电池转向 24 V IN和 48 V IN系统,适当抑制输入的需求变得更加重要。12V 电池系统通常使用额定电压为 40V 或更高的组件,以承受负载突降条件下的短时电压尖峰。这些 12 V 系统的直流电压可达 18 V DC。热插拔可能会导致输入振铃,电压接近输入的两倍,例如 36 V。这远低于 40 V 或更高额定值的组件。然而,在稳态输入电压可达 54 V 的 48 V 系统中,输入振铃可能超过 100 V,从而损坏额定电压为 80 V 的组件。 对于传统的 12 V 系统,人们通常假设阻尼电容器具有足够的有效串联电阻 (ESR) 来抑制谐振。但是,对于低成本铝电解电容器,实际有效 ESR 通常远低于公布的值,导致在使用电池供电时阻尼更小,振铃更大。对于 12 V 系统,降低的阻尼可能仍足以防止下游 DC/DC 不稳定,并且振铃不会造成损坏。然而,在更容易受到振铃影响的 48 V 系统中,您可以添加与输入阻尼电容器串联的分立电阻。根据稳态纹波电流,尺寸 0603(1608 公制)应该足够。 在图 1中,现有 DC/DC 转换器输入滤波器的 L1 和 C1 值产生由公式 1 表示的谐振: 
我们根据 TI E2E设计支持论坛技术文章“阻尼输入磁珠谐振以防止振荡”选择目标阻尼电容器 (C d ) 和阻尼电阻 (R d ) 。理想情况下, C d应该至少是C 1的三倍。我们为 C d选择 150 F 标准值。 公式 2 表示目标阻尼电阻:

对于阻尼电阻 (R d ),添加两个并联的 1 Ω 电阻与 C d串联。
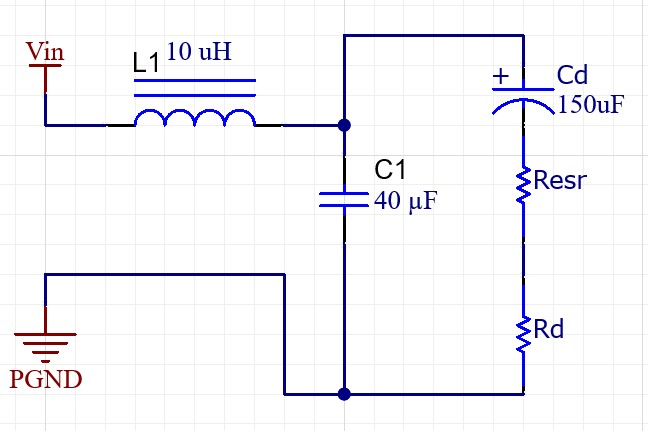
图 1带有阻尼功能的简化输入滤波器,可防止首次使用电池电源时出现过大的电压振铃,同时还可防止可能导致转换器不稳定的谐振。 图 2显示了在不添加和添加与 C d串联的 0.5Ω 阻尼电阻的情况下的模拟热插拔响应。
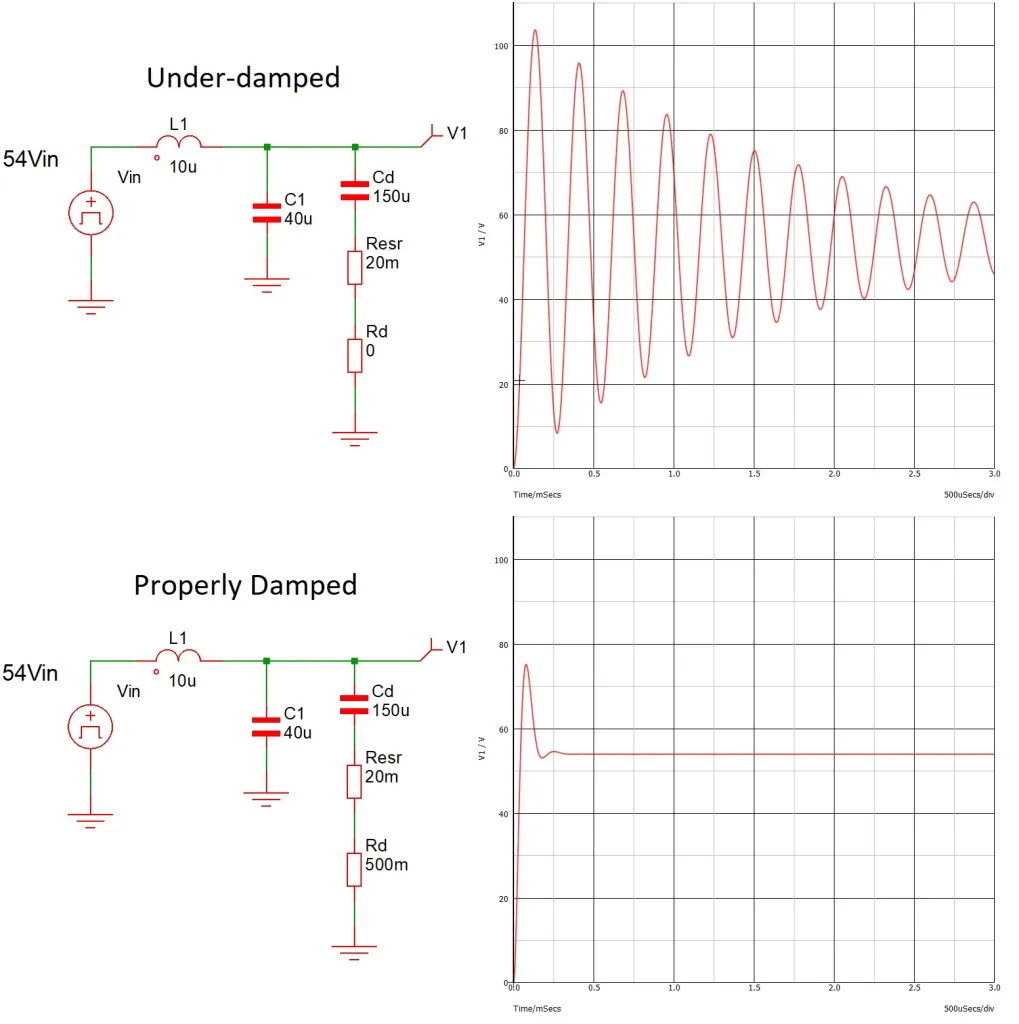
图 2不带和带阻尼 0.5Ω 阻尼电阻串联 C d的热插拔仿真。 我们通过使用正确的阻尼电阻器和电容器组合实现了输入滤波器的阻尼。然而,有一个方面很容易被忽视。在实验室中,我们经历了热插拔电源时阻尼电阻 (R d )的损坏。我们意识到阻尼电阻器的峰值功率由公式 3 表示:

对于 54 V 电压下的 1 Ω 电阻器,每个电阻器的峰值约为 2,900 W。此外,电阻器在很短的时间内消耗的能量几乎与阻尼电容器(C d )中存储的能量相同。阻尼电容器中存储的能量由公式 4 表示:
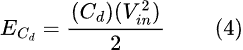
在我们的例子中,该能量在两个 1 Ω 电阻之间平均分配。54 V IN时 150 F 的电容总计约为 220 mJ,或每个 1 Ω 电阻器中的电容为 110 mJ。这是一个稍微严格的假设,因为 C d的内部 ESR将这些电阻器上的实际峰值电压降低了约 4%。 将实际浪涌映射到浪涌额定值图中的曲线并不简单。实际浪涌曲线大致呈衰减指数波形,而电阻器额定值假定固定持续时间的恒定功率,如图3所示。
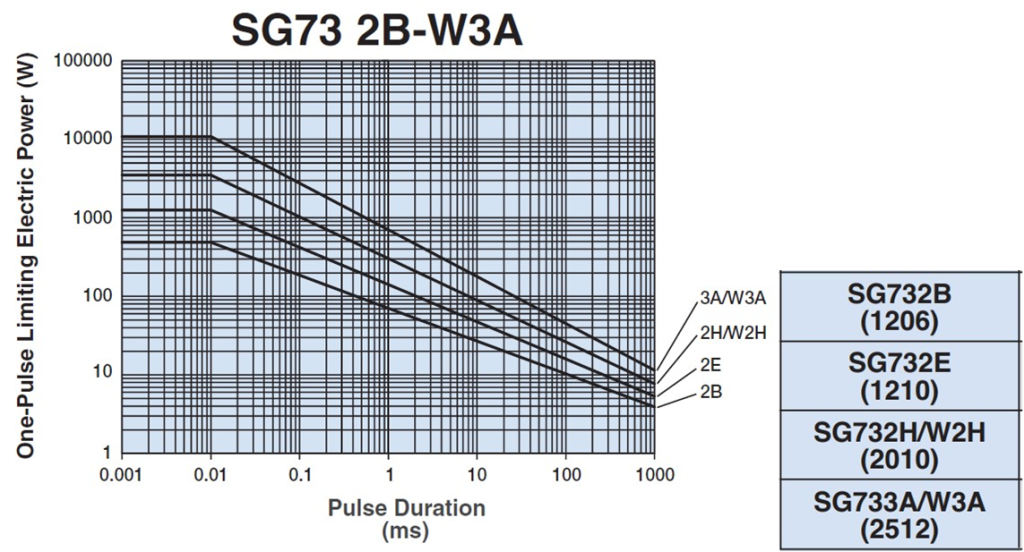
图 3浪涌额定电阻器额定值示例显示了大致衰减的指数波形。 保守的方法是将电阻器中消耗的总能量除以峰值功率。然后,您可以根据电阻器的浪涌额定值图检查产生的脉冲持续时间。计算出的脉冲将比实际脉冲更剧烈,实际脉冲是相同的加热能量分布在更长的时间范围内。对于我们的例子,在每个电阻器中,110 mJ 除以 2,900 W 等于 38 ?s。尺寸为 2512 SG733A/W3A 的额定浪涌电阻器可在大约 40 ?s 内处理 4.5 kW 的功率,这意味着该封装电阻器适合此应用。采用相同 2512 封装的通用电阻器的额定功率比浪涌额定电阻器低一个数量级以上。 该计算确实忽略了串联电感效应。电感器会减缓流入电阻器的电流上升速度并降低功率,但也会增加过冲造成的总损耗,如图 2 所示。包括 10 H 电感器在内的仿真结果显示,电阻器中的峰值功率从计算功率为 2.9 kW,但电阻器中的总能量比之前计算的 110 mJ 高 17%。额定值曲线显示,允许的能量遵循峰值功率比的负三分之二次方。因此,峰值功率降低 30% 会使损耗增加 27%,并且我们的计算对于没有串联输入电感和有串联输入电感都保持保守。 避免热插拔故障 虽然的汽车安装和维护实践将避免热插拔,但人们认识到这会发生错误。遵循本文所述的步骤将避免对系统造成代价高昂的损坏。作为您在电源管理领域的合作伙伴,TI 不断追求突破功耗极限。