在现代电子设备的应用中,许多场景要求开关电源不仅能够控制能量的双向流动,还需实现低压、大电流的输出。例如在可再生能源发电系统、电动汽车充电系统等领域,能量的双向流动控制至关重要。在开关频率不太高的情况下,随着输出电压的降低和输出电流的增加,整流损耗成为影响开关电源效率的主要因素。因此,降低整流损耗对于提高开关电源的效率至关重要。本文采用的同步整流技术便是一种有效的降低整流损耗的手段。
以往,在电源设计中,模拟控制技术因动态响应快、无量化误差、价格低廉等优点被广泛应用;而数字控制技术则因成本和技术等因素较少得到应用。近年来,随着半导体技术的飞速发展,数字微控制器的成本显著降低,性能大幅提高,使得高频开关电源的全数字化成为可能。数字控制具有简化系统硬件设计、减少分立元件数量、提高系统可靠性等诸多优势,未来必将在开关电源设计中得到更广泛的应用。
系统的整体构成如图 1 所示,虚线内为系统的控制部分,其余为主电路部分。主电路的工作原理将在后续详细分析。
系统控制电路的处理器是 PHILIPS(飞利浦)公司基于 ARM7 内核的 LPC2119 微控制器。LPC2119 具备高性能、低成本、低功耗等优点,非常适合对成本和性能要求严格的工业控制领域。负责 A/D 转换的是 24 位高精度的 A/D 转换器 CS5460A,它同样具有低成本、高性能的特点,在各类产品中应用广泛。
控制电路工作时,CS5460A 获取系统输出电压、电流量的模拟信号后,将其转换为数字量,并通过专用总线传给 LPC2119。LPC2119 对这些信息进行数字滤波等软件处理后,将其作为反馈量用于控制算法的运算,得到控制量及其相应的驱动信号,终控制主电路开关管的动作。
为简化控制电路结构、提高系统可靠性,系统采用以 ARM 芯片 LPC2119 为的全数字化设计。要实现期望的控制功能,除基本控制电路外,完善可靠的控制软件和恰当的控制策略必不可少。
在控制软件方面,按照层次分明、时序分级、全局考虑、书写规范的设计总则进行开发。程序整体分为 3 个层次,即主控层、算法层和接口层。接口层为底层,负责与硬件的接口,处理所有与外设有关的操作;主控层为顶层,不涉及具体操作,主要负责各个任务的调度、中断的安排以及时间和优先级的处理,包含 main 函数和中断函数,通过调用算法层的函数实现系统功能;算法层起到连接主控层和接口层的桥梁作用,负责具体任务的执行和控制算法的实现,系统的主要功能都在该层体现。
在控制策略方面,选择了增量式数字 PI 算法。该算法具有以下优点:一是不用做累加,控制量的确定仅与近几次误差采样值有关,误差不累积;二是每次输出的是控制量的增量,误动作影响小。在 PI 算法中,比例部分可改善系统的动态性能,积分部分能减小系统的稳态误差,理论上可实现无静差输出。离散化后的数字 PI 算法表达式为:

式中:KP 为比例系数;K1 为积分系数;e (k) 为本次误差;u (k) 为本次控制量输出。
由式 (1) 递推可得:

式 (1) 减去式 (2) 可得到增量式数字 PI 控制算法的表达式如下:

式 (3) 中的△u (k) 即为数字调节器输出的控制量的增量。所以,控制算法终输出的控制量为:

在装置实际工作中,若负载为铅酸蓄电池,当能量正向流动(充电)时,系统可根据需要分别采用电压闭环或电流闭环控制装置的输出电压和输出电流,电压、电流闭环采用上述增量式 PI 算法;当能量反向流动时,出于实际应用需要,系统只对负载(蓄电池)侧进行恒流控制。
本文提出的主电路拓扑如图 2 所示,主要包括电源输入侧滤波电容 C1、主开关管 S1 以及由 R1、C2、D2 组成的 S1 的 SNUBBER 电路、变压器 T 以及为其原边进行磁复位的第三绕组和为其副边进行磁复位的由 R2、C3、D3 组成的钳位电路、整流管 S2、续流管 S3 和输出滤波环节 L 及 C4 等部分。
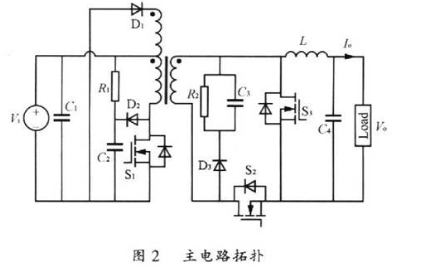
为便于分析,假设负载为一只蓄电池。电路控制能量正向流动时,主电路每周期的工作可分为正向流动阶段和续流阶段。为防止整流管 S2 和续流管 S3 同时导通造成变压器副边的贯穿短路,两管的互补脉冲需加入死区,因此电路的工作过程可分为 4 部分。主管 S1、整流管 S2、续流管 S3 的驱动信号如图 3 所示,图 3 中的 1 至 4 分别对应电路工作的 4 个阶段。
当能量正向流动时,若输出电流流过管压降较大的 MOS 管寄生体二极管,会带来较大的整流损耗和续流损耗。为此,应用同步整流技术,使电流流过导通电阻只有 6mΩ 的 MOS 管,大大降低了损耗,提高了效率。以下是能量正向流动时 4 个工作阶段的详细分析:
阶段 1(能量正向流动):此阶段开始时,主管 S1 和整流管 S2 被触发导通。输入电流流入变压器原边绕组的同名端,输出电流流出变压器次边绕组的同名端。此时能量由输入侧向负载侧传输的方式与传统的单端正激变换器基本一致,其电流流向如图 4 (a) 所示。图 4 (a) 中的 i1 代表变压器原边电流,i2 代表变压器副边电流(下同)。此过程直到主管关断时结束。
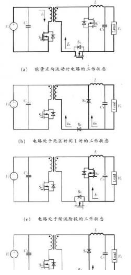
阶段 2(死区时间 1):此阶段刚开始时,主管 S2 和整流管 S2 关断,续流管 S3 仍未导通但其体二极管已经导通。由于变压器漏感的限制,变压器副边的电流由输出电流逐渐减小,而流过续流管体二极管的电流则由零开始逐渐增大。在此阶段中,输出电流在由整流回路向续流回路转换。此过程电流方向如图 4 (b) 所示。图 (b) 中的 i2a、i2b 分别表示负载电流流经整流管和续流管的两部分。
阶段 3(续流阶段):此阶段开始时,续流管 S3 被触发导通,输出电流主要经由 S3 续流,损耗大为降低。此阶段将持续到续流管 S3 关断时结束,其电流流向如图 4 (c) 所示。
阶段 4(死区时间 2):此阶段刚开始时,续流管 S3 关断,但其体二极管仍导通续流。输出电流完全经由续流管的体二极管进行续流。此阶段直至主管导通以后才中止。此过程电流方向如图 4 (d) 所示。至此,主电路一周期的工作结束。当电路下动作时,主管 S1 和整流管 S2 又会导通,电路重新进入阶段 1 的工作状态。
在能量反向流动时,电路的工作过程与 BOOST 电路基本一致,可大体分为两个阶段:
综合考虑电源体积、系统效率、控制精度、器件耐压等诸多因素,本文选取的工作频率 f = 55 kHz,T = 1/f,占空比 Dmax 为 0.4,则主管 S1 的导通时间 toNmax 为:

实验中,整流管和续流管选用 IRL3803,变压器原边磁复位电路中所用的二极管为 PHILIPS(飞利浦)的 BYV26G。在进行整流管和续流管的选型时,除考虑功率器件的耐压、通流能力外,还需特别关注导通电阻值的大小。本文选择的 IRL3803 是 IR 公司推出的专门用于同步整流的 MOS 管,导通电阻只有 6mΩ,能够减小导通损耗和发热。由式 (5) - 式 (14) 计算可得变压器原边、副边、第三绕组的变比为 170:3:255;输出滤波电感为 14.72μH;电容为 9900μF。负载为单体铅酸蓄电池。
实验主要技术条件如下:开关频率为 55kHz。正向工作时,输入电压 Vi 为 400 (1 ± 5%) V,额定输出电压 Vo 为 2V、输出电流为 20A;反向工作时,输入电压为 2 (1 ± 10%) V。
经测量,系统工作时稳压、稳流精度均可达到小于 0.5% 的设计要求;装置效率为 86.7%。主要实验波形如图 6 - 图 8 所示;能量正 / 反向流动时,系统的效率曲线如图 9 所示。
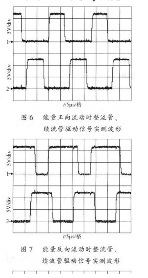
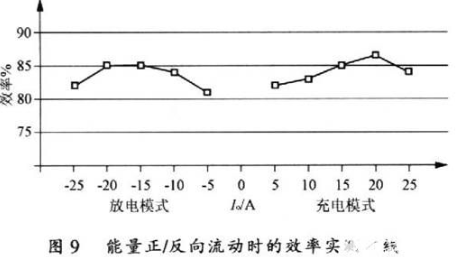
图 6 为给蓄电池充电时整流管、续流管驱动信号的实测波形。此时原边主管波形与整流管完全同步。图 6 中通道 1 为整流功率器件的驱动波形,通道 2 为续流功率器件的驱动波形。图 7 为能量反向流动时,整流功率器件、续流功率器件的驱动信号实测波形,此时原边主功率器件不动作。图 7 中通道 1 为整流功率器件驱动波形,通道 2 为续流功率器件驱动波形。图 8 为能量正向流动时,DC/DC 变换器输出 2V 电压的实验波形。从图 8 中可看出,输出稳压精度高,电压纹波很小。