传统上采用笨重 DBC 模块封装的功率 WBG /SiC 器件可以用近芯片级 SMD 封装替代。WBG 器件的芯片尺寸更小(功率密度更高)且效率更高,因此可以实现这种替代。MaxPak 等近芯片级封装可以减小封装尺寸和寄生效应,使SiC 器件能够以性能、效率和速度运行。
这些器件进一步实现了更高密度的平面系统,提高了系统性能和效率。Power MaxPak 器件可以在系统组装之前进行全面预测试,从而降低复合产量损失和组装成本。MaxPak 是一种专有的 Power QFN 封装,采用自动化低成本 QFN 组装技术,可提高产量并进一步降低制造成本。我在 2018 年 7 月的 Bodo's Power Systems 文章“Power GaN 和 SiC 近芯片级 SMD 封装的必然性”中解释了 ?MaxPak 类型封装的要求。
MaxPak Near ChipScale 封装中的 SiC
开关可以为重工业设备、电动汽车和机车牵引供电。MaxPak 开关的横截面示例如下图 1、2 和 3 所示。功率较高的产品非常薄,因此厚度不是按比例绘制的,而且为了展示关键的结构特征,厚度被夸大了。
个重点是轻工业电源开关
MaxPak 初的重点是 650V/400A 和 1200V/200A 工业开关。芯片尺寸受限于直接焊接到电源 PCB、DBC 基板甚至厚铜引线框架的可焊性,从而限制了电流。初始 MaxPak 设计、类型
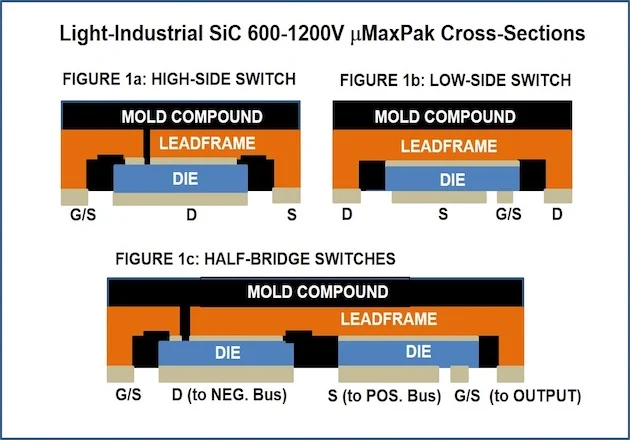
图 1:轻工业 SiC 600-1200V MaxPak 横截面
顶部/左侧:高端开关 顶部/右侧:低端开关
底部:半桥开关
I 和 II 将所有热和电连接从 SiC 芯片的顶部和底部带到 SMD 封装的底部。它们可容纳横向 GaN 和垂直 SiC 芯片。近芯片级 SMD 是用于封装 600-1200V IGBT 开关的 DBC 模块的显著先进替代品。这些模块体积庞大、速度慢且价格昂贵,尽管它们巨大的寄生效应对于硅功率器件来说是可以接受的,但它们极大地限制了功率 WBG(GaN 和 SiC)器件的性能。图 1 显示了工业 ?MaxPak a) 高端、b) 低端和 c) 半桥开关的基本结构。
对于 I 型和 II 型 ?MaxPak SMD 封装,封装底部的焊盘面积限制了可用空间和电流,而可用的焊盘间距限制了电压。随着新型 III 型 ?MaxPak 顶部和底部焊盘的不断发展,它们可用于扩展工业 600V-1200V 产品的电流范围。对于轻工业 ?MaxPak 来说,所有底部焊盘都适用于标准 SMD 组装工艺,这非常有利。
可扩展至电动汽车 (EV) 牵引力更高电流:III 型或薄型 ?MaxPak 消除了封装顶部的过度成型,可在底部和顶部使用电垫和导热垫,可容纳 750A 及更高的电流。成型操作本质上是填充双面蚀刻引线框架中的开放空间。此成型操作要求引线框架和模具设计为适合模塑料填充和流动。III 型 ?MaxPak 的双面垫还需要对两侧进行去毛刺和电镀。
III 型 MaxPak 封装需要垂直 WBG 芯片,如 SiC MOSFET,其漏极 (D) 位于一侧,源极/栅极 (S/G) 位于另一侧。(如果 D 通过通孔被带到芯片的背面/另一侧,则可以使用当今的 SiC 衬底上的横向 GaN。)更大的顶部和底部焊盘可容纳 600V-1200V EV 牵引开关的更高电流。图 2 显示了 EV ?MaxPak 的基本结构 a) 高端 (HS) 和 b) 低端 (LS) 开关。
更高的 EV 电流会增加所需的芯片尺寸,因此必须将MaxPak 焊接到 DBC 基板隔离器上,以尽量减少与暴露的底部芯片的 CTE 膨胀失配。这些基板必须提供具有高压隔离的热阻。
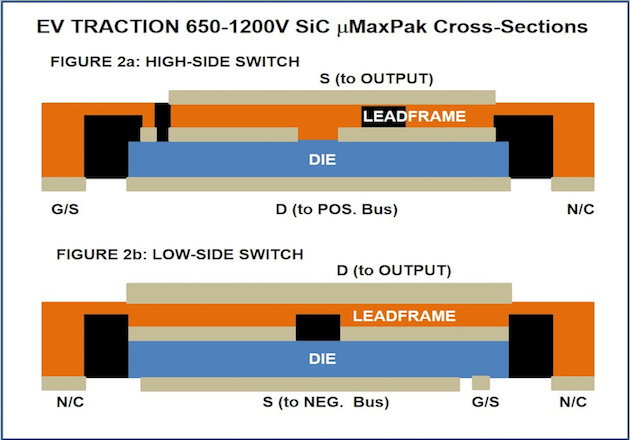
图 2:EV 牵引 650-1200V SiC ?MaxPak 横截面
顶部:高端开关 底部:低端开关
HS & LS ?MaxPak 开关的顶部将焊接到输出总线上,这又存在暴露的 SiC 芯片和铜输出总线之间的 CTE 不匹配问题。因此,大电流
触点需要多个焊盘,焊盘之间具有应力释放功能。应力释放可以通过多个薄而窄的连接器和 C 形弯头来实现。
对蚀刻引线框架条进行二次成型或压印操作可以产生应力释放和高压间隙特征。此操作可实现一体式功率 QFN 引线框架,这是美国 9,214,416 中描述的 ?MaxPak 腔体架构的一个关键特性。
更高功率的近芯片级封装,顶部和底部均带有电源焊盘,采用基本的 QFN 技术和专有的 ?MaxPak 腔体结构构建。然而,引线框架设计需要增强的模塑料流动和锁定功能以及更薄的封装。更高电流 SiC ?MaxPak 牵引开关配置的基本概念如图 2 a 和 b 所示。
可扩展至高压机车牵引更高的电流和电压
机车牵引开关也是 TYPE III ?MaxPak,顶部和底部都有外部焊盘,以适应大型芯片和高电流。机车牵引还需要更高的电压能力,如 3.3kV-6.5kV。虽然机车 ?MaxPak 引线框架条包含相同的 SiC 芯片专有底部腔体,但在 QFN 分离操作期间,模塑后腔壁被移除。这种分离操作方便地将高压漏极留在封装的一侧,将低压源和栅极留在另一侧。当在动力传动系统中灌封或涂覆时,这可以在 ?MaxPak 封装外部提供污染等级 1 的爬电路径。
在 MaxPak 中,芯片边缘的高压漏极接近芯片另一侧的低压 G/S 平面。因此,隔离需要在 G/S 侧的 HV 芯片边缘和焊接引线框架或 DBC 铜垫之间使用更厚的模塑料。这在 HS 开关中通过更深的引线框架压印或成型来实现。在 LS 开关上,G/S 引线焊接到底部 DBC 铜垫,因此必须通过使用焊料和电镀抬高芯片来分离芯片边缘以增加分离。分离处填充有封装模塑料,封装下方填充有系统灌封材料。详细信息请参见图 3a 和 3b。

图 3:机车牵引 SiC MaxPak 横截面
顶部:高端开关 底部:低端开关
电力机车牵引应用需要 MaxPak 可扩展至 1000A 电流和 3.3kV 及更高电压。如今,电动汽车和机车应用迫切需要这种功率 SiC 器件的性能和效率,而 MaxPak 可使 SiC 发挥其全部固有性能和效率。
MaxPak 图像和视角
MaxPak 近芯片级 SMD 封装通常厚度约为 1 毫米,仅略大于总功率芯片面积。请参见下面的MaxPak 单开关 (SS) 和半桥 (HB) 的 3-D 视图。图 4a 显示了带有 SiC MOSFET和
二极管芯片的 HS-SS MaxPak 的顶部,图 4b 显示了带有 MOSFET 和二极管芯片的 HB MaxPak 的顶部,HS 和 LS 开关中都有 MOSFET 和二极管芯片。HS-SS 可以翻转成为顶部带有阳极 (A) 和漏极 (D) 焊盘的 LS-SS。
图 4c 显示了 3.3kV 750A SiC MaxPak 单开关与典型信用卡的尺寸对比。这是极好的对比,因为 MaxPak 封装和信用卡的厚度均为约 1 毫米。
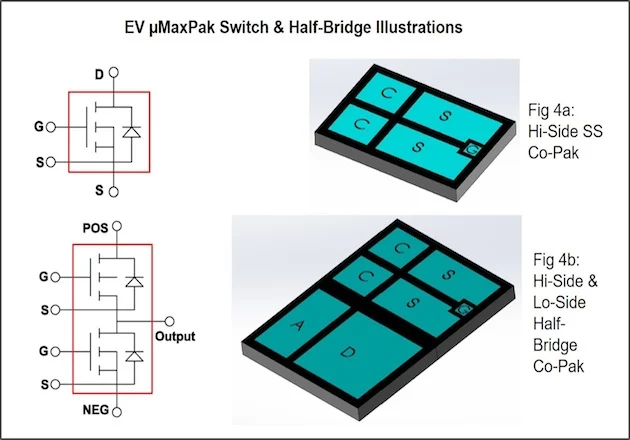
图 4:EV MaxPak 开关和半桥示意图 顶部:高侧 SS Co-Pak 底部:高侧和低侧半桥 Co-Pak
使用 MaxPak SiC 开关进行电动汽车和机车牵引
电动汽车和机车牵引动力传动系统或电机驱动架构必须且应该不断发展,以实现完整的 SiC 性能、效率和速度。如果将所有电感放回动力传动系统结构和内部连接中,那么消除过时的 IGBT DBC 模块的引线键合、引线和
端子是没有用的。近芯片级 SMD 封装几乎消除了开关封装寄生效应,几乎保持了未封装芯片的功率密度。它们提供经过预先测试和生产的开关,带有多个芯片(MOSFET 和二极管),可以在不损坏的情况下进行处理和组装。

图 4c:机车 3.3kV_750 A SiC ?MaxPak 开关
动力传动
逆变器现在可以是平面 SMD 组件,同样没有笨重的端子和少的互连。此外,平面引线还可以提供电感消除。理想情况下,所有其他电源组件都可以消除或化互连,并且仅使用端子退出驱动系统。设计驱动系统结构超出了本文的范围。本文的重点仅限于说明使用 ?MaxPak SMD 封装开关的 SMD/平面三相逆变器。逆变器示例解决了 MaxPak 电气和热接口问题,并展示了如何简化其他电源驱动组件,以实现未来整个系统的更高功率密度、性能和效率。
参见图 5,平面/SMD 逆变器带有六个MaxPak 开关,位于底部冷板上。三条输出总线显示为焊接到三个 HS 和 LS 开关对的铜条。这种方法简单易懂,但这种配置仅从 ?MaxPak 开关的底部吸收热量。如果使用 DBC 基板进行隔离,也可以从三个输出总线中散热。这种配置提高了 SiC 冷却和性能,但也可能增加电气和热互连的复杂性。

图 5:带有六个 MaxPak 开关的平面/SMD 电动汽车逆变器示意图
尽管 MaxPak 封装由 SiC 开关的性能、效率和速度驱动,但它们也极大地减少了电动汽车和机车驱动装置的尺寸、重量和冷却系统。