基于 BLDC 的逆变器系统广泛应用于冰箱、洗衣机、烘干机、房间空调和风扇电机等消费类应用,因为它比使用直流电机或交流感应电机的传统解决方案更快、更安静、更节能。如今,由于节能和法规要求,它的需求和扩展已成为强制性要求。推动这一进步的关键技术是逆变器技术,特别是传递模塑集成
功率模块。
自 1998 年以来,转移模塑封装技术已成功应用于使用IGBT、续流 FRD 和 MOSFET 作为电源开关以及使用高压
集成电路 (HVIC)作为栅极驱动器的电机驱动 IPM [1]-[6]。IPM 的电压和电流范围已陆续增加到 1200V 和 50A 以上。转移模塑技术的优势主要在于同时使用铜引线框架作为电导体,这可以大大减小封装尺寸以及制造成本。
家用电器空调和净化系统中使用的低功率 BLDC 风扇电机逆变器设计由于数量巨大且产品空间有限,对成本和尺寸限制要求非常严格。通过将横向 IGBT 与控制电路集成在单个硅片上,已经针对此应用开发了多项单芯片逆变器解决方案。它们可以提供更小的电路面积,但也存在一些缺点。电路设计缺乏灵活性,而且功率耗散集中在一个位置,这会导致热管理问题。LIGBT 的开关性能和耐用性低于传统开关器件,导致应用范围和可控性非常有限。
对于这些小型风扇电机驱动应用,Alpha and Omega Semiconductor 开发了一种新型表面贴装 IPM。建议的模块由采用新封装的先进 MOSFET 和栅极驱动 IC 组成,是一种高度紧凑、可靠且经济高效的解决方案。由于采用了部分超结 MOSFET 技术、集成自举电路的 HVIC 以及优化的封装设计,IPM 的封装尺寸极小,因此可以显著提高系统的成本效益开发,减小逆变器电路板尺寸,实现简单可靠的 PCB 组装。
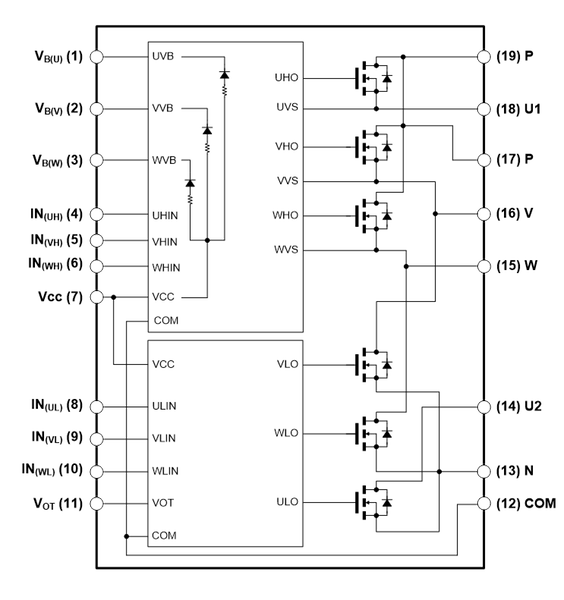
图 1:建议的 IPM。(a)外部视图,(b)内部等效电路和引脚配置
紧凑的封装和电气设计
图 1(a) 显示了所提出的双列直插式 IPM 的 19 引脚计数封装的轮廓。采用了引线框架结构,并在其上焊接了多个 MOSFET 芯片和栅极驱动 IC。此封装所需的总表面为 18mm x 10.3mm = 185.4mm2(包括引脚引线)。分立解决方案采用三片 SO-8 封装的 HVIC 半桥驱动器,每个驱动器的表面需求为 5mm x 6.2mm = 31mm2,六片 DPAK 封装的功率器件,每个器件的表面需求为 6.5mm x 10mm = 65mm2,需要 483mm2(= 3x 31mm2 + 6 x 65mm2)的表面。因此,保守地总结尺寸优势(忽略复杂布线的空间)与分立解决方案相比,PCB 空间需求仅为其 38%。图 1(b) 示出了内部等效电路和引脚配置,该电路由六个 MOSFET 作为功率开关器件、包括集成自举元件的高端栅极驱动 HVIC 和包括温度传感 (VOT) 和固定过温保护功能的低端栅极驱动 LVIC 组成。信号 COM 位于电源地 N 端子处。有两个 u 相输出引脚 U1 和 U2,需要通过外部 PCB 布线连接。
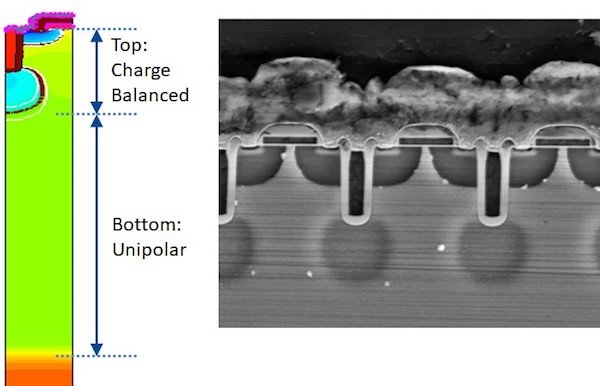
图2:新型MOSFET的垂直结构
图2显示了集成在IPM中的新型MOSFET的垂直结构。它是专为具有部分超结配置的电机驱动应用而新开发的。与传统平面MOSFET相比,功率密度Rds·A提高了30%以上,并且与超结器件相比,它可以提供更合适的EMI可控性。
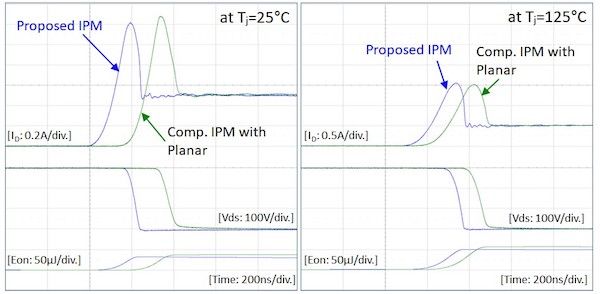
图 3:开启开关行为
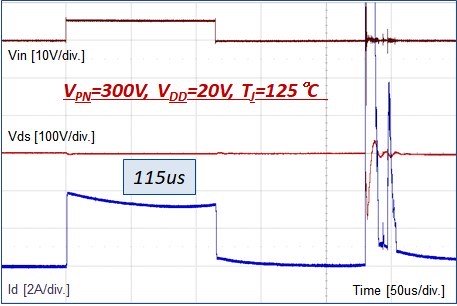
图 4:短路耐受性
通过微加工和晶圆工艺技术,设计的部分超结 MOSFET 实现了适当的导通开关性能。从图 3 所示的实验波形中,我们可以清楚地看出,在 EMI、噪声和功耗方面,Irr、Qrr 和 trr 性能与三相电机驱动应用中使用的传统平面 MOSFET 技术相当。已对栅极
电阻器 Qg 和 Vth 进行了选择和设计,以防止导通时的击穿问题。
图4显示了MOSFET短路耐久性的评估波形。它显示超过100us的耐受时间,这对于逆变器的稳定设计和控制来说已经足够好了。
已根据包括寄生电路电感在内的实际 IPM 逆变器电路条件评估了开关操作 SOA。尽管所提出的 IPM 的额定电压为 500V,但受 MOSFET 击穿电压 (BV) 限制,我们已将施加的直流链路电压提高到 600V 以上。为了保证 500V,MOSFET 的典型 BV 设计基于 550V。值得注意的是,由于 MOSFET 设计非常坚固,在直流链路电压为 550V 的条件下,开关操作中没有任何异常现象,如图 5 的波形所示。当我们施加超过 600V 的直流链路电压时,由于部分直通电流,观察到出现异常导通电流。但由??于短路强度高,IPM 没有发生破坏性故障。

图 5:开关 SOA 测试
高精度温度转换电路已通过激光微调技术集成到嵌入式栅极驱动 LVIC 中。VOT 引脚生成与 LVIC 温度相对应的模拟输出电压信号。可以在更接近可容忍额定值的结温下使用 IPM。图 6 说明了 VOT 的输出特性。对不同批次的样品进行了评估,以验证 VOT 性能在实际应用条件下的容差。值得注意的是,LVIC
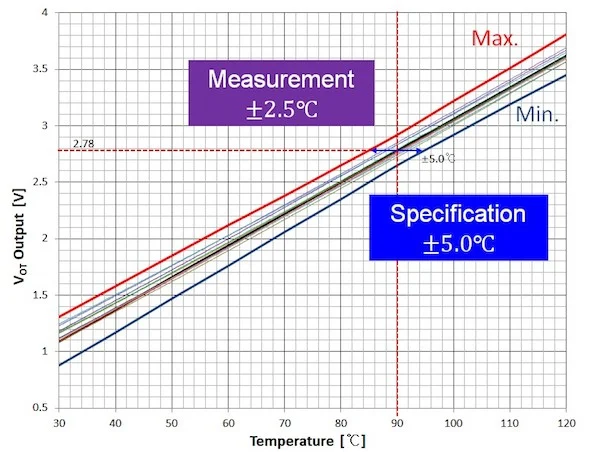
图 6:建议的 IPM 的 LVIC 温度输出
通过LVIC的合理设计及其精密的晶圆工艺,可以测量温度。由于所提出的IPM封装尺寸很小,VOT的电压输出将根据MOSFET的结温做出快速响应。它可为应用提供简单、廉价且准确的解决方案。
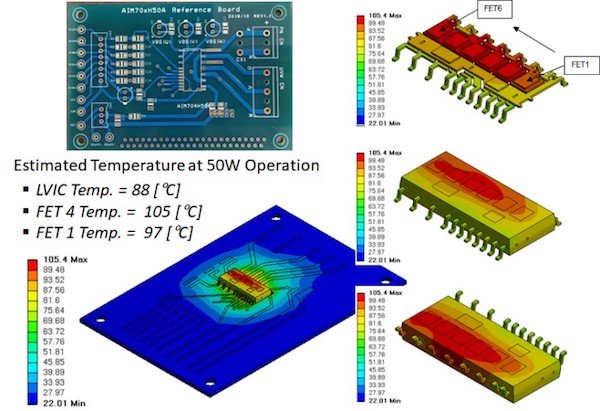
图 7:fSW=20kHz、PF=0.8、VDC=300V、VCC=15V 时的工作热模拟
申请考虑
考虑到 50W-BLDC 电机的工作条件,进行了热仿真。采用了 20kHz 的 PWM 开关频率,这被视为现场的正常频率,以避免可听见的噪声。从图 7 所示的仿真结果可以看出,FET 4 的结温,而低压侧 FET 1 的温升。两个 MOSFET 芯片之间的温差为 8°C。可以说,模块的额定功率将受到 FET 3 和 FET 4 的中心芯片的限制。在应用的工作条件下,LVIC 温度比 FET 4 低 17°C。
图 8 解释了所提出的 IPM 应用示例的仿真摘要,其中仿真是基于连续工作功率条件进行的。在图 8(a) 中,功率损耗是在结温为 150°C 时计算的。假设 FET 4 的工作结温决定了额定功率。应该注意的是,允许的工作功率由外壳温度 Tc 决定和控制,如图 8(b) 所示。LVIC 和 FET 4 之间的温差可能达到 30°C 以上,具体取决于工作功率,如图 8(c) 所示。在模块设计中,固定 OT 保护水平通常为 LVIC 温度的 130°C。图 8(d) 表明 FET 4 的温度略高于 FET 3。图 9 说明了应用电路示例和实验设置。可以通过将 10kΩ 下拉电阻连接到 VOT(引脚编号 11)来禁用内部固定的过温保护功能,或者通过不连接电阻来启用。无论下拉电阻连接如何,用于检测 LVIC 温度的模拟电压输出 VOT 始终处于激活状态。建议使用 R2-C5 (2kΩ-10nF) 滤波器,以避免温度传感功能因噪声而发生故障。图 10 显示了红外摄像机拍摄的温度曲线。结果表明,在 50W 逆变器运行时,MOSFET 芯片中心区域的温度比 LVIC 部分的温度高出约 14°C。

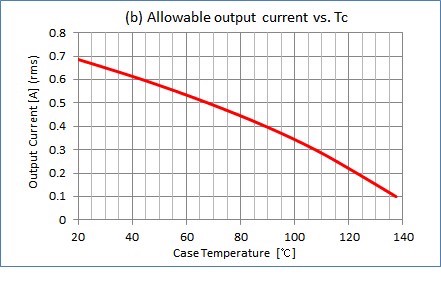
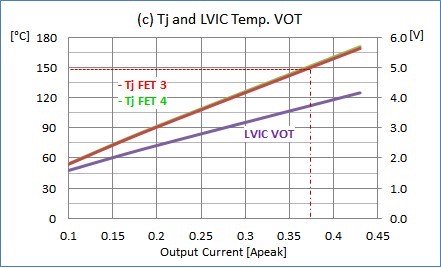

图 8:模拟结果。(a)功率损耗,(b)允许工作电流,(c)温度上升,(d)温差
图 11(a) 显示了启用 OT 保护功能的实验结果。当 LVIC 温度达到其跳变水平(典型值 130°C)时,OTP 被激活。此时,测量的外壳温度 Tc 为 144°C。当 LVIC 温度降至其复位水平(典型值 100°C)时,OTP 操作被停用。显然,30°C 的 OTP 滞后水平是经过设计的。
还通过将 10kΩ 下拉电阻连接到引脚 11 来测试禁用 OT 保护情况下的温升,如图 11(b) 的测量结果所示。观察到当外壳温度 Tc 达到 160°C 时,LVIC 温度达到 144°C。出于安全考虑,逆变器系统已被故意关闭。
IPM 应用的另一项有趣研究是自举电容电压的变化,如图 12 所示。逆变器输出频率为 60Hz,开关频率为 20kHz。自举电压与输出电流一起表示
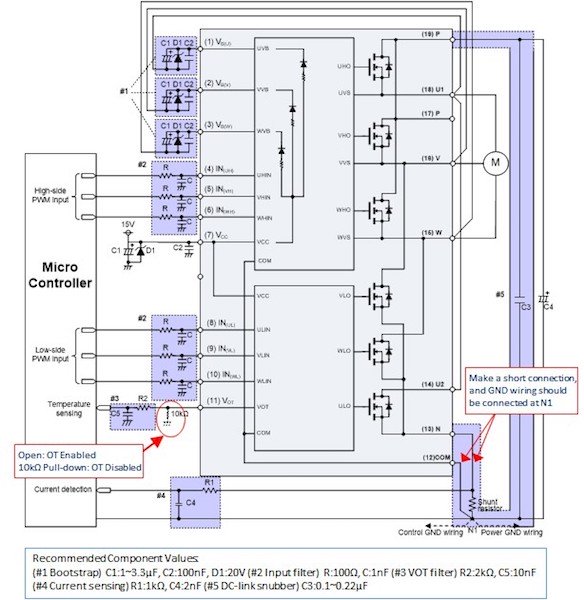
图9:应用电路示例
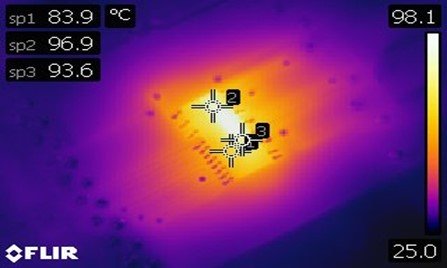
图 10:红外摄像机拍摄的温度曲线
逆变器的自举电压VBS在正电流时上升到接近VCC=15V,但在CBS=1uF时下降到接近13V。这是由于电流方向不同的充电机制造成的。输出电流为正时,电流要么流经高端MOSFET,要么流经低端体
二极管。此时,低端体二极管导通时,自举电容CBS充电。如果充电过程中体二极管电压VSD不高于自举二极管的正向压降,则MOSFET IPM中的充电峰值电压将略低于VCC电源。输出电流为负时,当低端MOSFET作为有源开关器件时,充电电压将下降到与MOSFET的正向压降一样多。但是,自举电压是高端MOSFET的栅极驱动电源,只有当电流为正时才至关重要。当电流为正时,由于 MOSFET 的 VSD 较低,自举电压不会发生很大变化,因此无需使用大型自举
电容器。只有当输出电流为正时,才可以使用足以将自举电压保持在 HVIC 待机电流范围内的小型自举电容器。在建议的 IPM 中,高端 UVLO 的设计典型值为 10V。
结论
我们介绍了一种新型超紧凑型表面贴装 IPM,用于家用电器中的低功率 BLDC 风扇电机驱动系统,其中主要关注的是耐用性、温度保护、功率耗散、电磁干扰、抗噪声和降低成本。尽管小型 MOSFET-IPM 已经达到一定的成熟度,但仍有一些问题需要解决,以进一步提高其性能并降低其成本。此外,IPM 技术及其应用方面的进步不断开辟新的发展趋势和工业兴趣。预计所提出的 IPM 可以显著增强逆变器板的简易性和可靠性设计,并可以提供相当经济高效的系统解决方案。
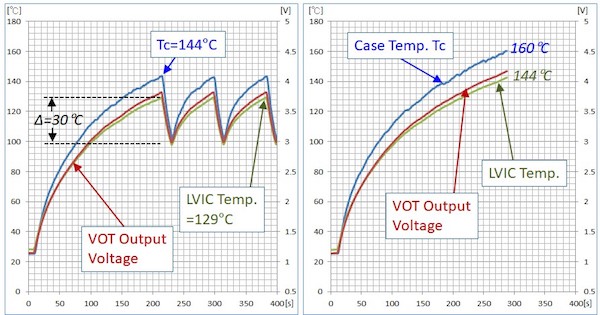
图 11:过温操作。(a)启用 OT,(b)禁用 OT
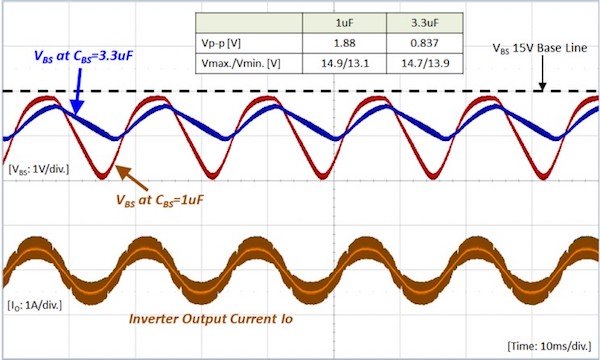
图 12:自举电容电压的变化