摘 要:锂离子电池的众多优点使其在手提式设备中获得了广泛的应用。但与镍铬、镍氢电池不同的是锂离子电池必须和保护芯片配合使用。本文提出了一种单节锂离子电池保护芯片的设计,此芯片能有效防止锂电池应用中发生过充电、过放电和过电流状态。
关键词:锂离子电池;过充电;过放电;过流;待机状态
前 言
锂离子电池保护芯片的设计与其封装结构密切相关,如图1所示为封装在锂离子电池内部的保护电路的基本结构。在正常情况下,充电控制端CO 和放电控制端DO 为高电位,N型放电控制管FET1和充电控制管FET2处于导通状态,电路的工作方式可以是电池向负载放电,也可以是充电器对电池进行充电;当保护电路检测到异常现象(过充电、过放电和过电流)时,使CO或DO输出低电平,从而切断充电或放电回路,实现保护功能。
为了有效利用放电电流或充电电流,FET1和FET2采用导通电阻很小的
功率管。它们的选择原则除了导通电阻要小,还要求体积小,并且关闭时源漏击穿电压要能经受不匹配充电器的影响。从理论上说,FET
1和FET
2可以用N 管也可以用P 管。但由于单节锂离子电池保护电路的电源电压较低,为了减小导通电阻,一般都采用N管。图1中
二极管是FET
1和FET
2的寄生二极管,它们的存在使系统在过放电状态下能对电池充电,在过充电状态下能对负载放电。
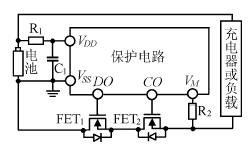
图1 3.6V 锂离子电池保护电路封装结构
锂离子电池保护芯片的应用场合要求其具有低电流驱动、高检测的特点,另外由于保护电路的供电电源即为电池电压,因此在电池电压的变化范围内,保护电路必须正常工作,本文根据图1 所示的连接关系,设计一种低功耗单节锂离子电池保护芯片,其电池电压可以在1V—5.5V范围内变化。
系统结构设计 锂离子电池保护芯片的基本功能是进行过充电保护、过放电保护和过电流保护,其中过电流保护包括充电过流保护和放电过流保护。下面以保护电路的基本功能为出发点,分析其系统的组成。
检测异常现象
锂离子电池保护电路为了实现其基本功能,首先需要检测异常现象。过充电和过放电检测是将电池电压进行分压(采样)后与基准电压比较实现的;而对于过流检测,保护芯片首先将充放电过程中的电流转化为在功率管FET
1、FET
2上的电压,然后通过V
M与基准电压比较完成,放电过流检测的是正电压,充电过流检测的是负电压。
滤除干扰信号 通常在锂离子电池保护电路的工作过程中会有干扰信号存在,干扰信号的类型主要有两种:一种为瞬间干扰,它是指在正常的信号上,在极短的时间内叠加上一个较大的信号。另一种为波动干扰,它是指信号的起伏波动。如图2 以充电过程解释了这两类干扰,其中V
CU 为过充电检测电压。
为了防止干扰信号的引入使保护电路产生误动作,可以从系统角度考虑采用适当的措施减小它们的影响。
瞬间干扰可以在保护电路内部加上延时电路加以滤除,即当保护电路检测到异常信号后,延时一段时间再关闭FET
1或FET
2。根据过充电、过放电、过电流对锂电池的危害程度选取不同的延时时间。为了更加合理的保护锂电池,放电过流可分为三个级别,分别为过流1保护、过流2保护以及负载短路保护,过流1的延时稍长,过流2的延时比过流1的延时短一些,而负载短路不加延时立即保护。波动干扰可以在保护电路内部加上迟滞电路加以滤除。
控制充电控制管有效关闭 在充电过程中,与FET
2源极相连的V
M端电位为负值,当过充电保护起作用时,必须在过充电延时信号与CO端之间加上电平转换电路,将控制
逻辑电路产生的逻辑信号进行转换,使CO端的电位小于或等于V
M端的电位,从而保证FET
2有效关断。
0V电池充电抑制功能 锂离子电池保护电路可实现对0V电池进行充电,也可实现对0V 电池禁止充电,本文的设计采用后者,这一功能使保护电路禁止对内部短路的电池进行充电。当电池电压为0V电池充电抑制电压V
OINH(典型值为1V左右)或更低时,FET
2的栅极电位被固定为V
M 的电位,从而禁止充电。当电池电压等于或高于V
OINH 时,可以进行充电。
其它功能 1)在过充电状态下,保护电路需禁止放电过流保护起作用。因为电池在过充电后接上负载的情况下,在放电初期,系统仍处于过充电状态,此时放电电流必然很大,引起过流的可能性很大;而过流保护如果起作用,就会关断放电回路。这样,一旦电池过充电,就可能永远不能使用;
2)在过放电保护起作用时,保护电路需禁止充电过流保护起作用。因为当电池过放电后,刚接上充电器充电时,充电电流会很大。此时禁止充电过流保护起作用,可保证电池在过放电后可充电;
3)为了减少充电电流流过FET
1内部寄生二极管的时间,如果在过放电状态下连接上充电器并且V
M电压低于充电过流检测电压时,解除过放电迟滞。
根据上述分析,本文设计的锂离子电池保护电路的系统框图如图3所示。系统主要包括控制逻辑电路(CONTROL LOGIC CIRCUIT)、取样电路(SAMPLE CIRCUIT)、过充电检测比较器(OVERDIACHARGE COMPARATOR)、过放电检测比较器(OVERDISCHARGE COMPARATOR)、过流1检测比较器(OVERCURRENT1 COMPARATOR)、过流2 检测比较器(OVERCURRENT2 COMPARATOR)、负载短路
检测电路(LOAD SHORT DETECTION CIRCUIT)、充电过流检测电路(CHARGER DETEDTION CIRCUIT)、电平转换电路(CONVERTOR CIRCUIT)、基准电路(REFERENCE CIRCUIT)以及偏置电路(BIAS CIRCUIT)。其中,偏置电路在图3 中没有给出,电平转换电路同时能实现0V 充电抑制功能。
图2 主要干扰类型
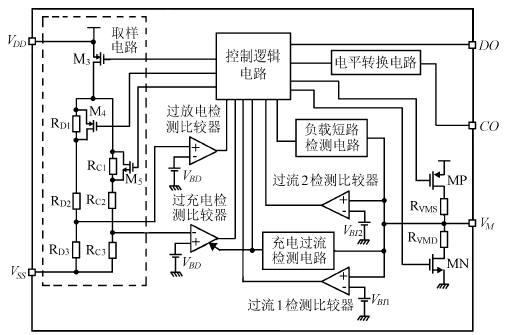
图3 锂离子电池保护电路系统框图
图3 中MN 在过电流时导通,它的作用是使过大的电流不经过FET
1和FET
2而通过MN流向地。MP与待机状态有关,待机状态电路的工作原理是:当保护电路进入过放电状态后,产生一个待机状态信号,使保护芯片中的大多数电路停止工作,它是通过控制逻辑电路和负载短路检测电路的配合完成的。M
3的作用是在待机状态下,使采样电路不消耗静态电流。M
4和M
5分别用于实现过放电和过充电检测迟滞以滤除充放电过程中的波动干扰信号。而瞬时干扰信号的滤除由控制逻辑电路中的延时电路实现。
关键电路实现 锂离子电池保护芯片的性能,不仅与系统结构密切相关,与具体电路的实现也是密不可分的,下面的电路模块在整个芯片中具有关键的作用,本文从功耗和等角度考虑,提出了独特的设计方法。
待机状态电路 保护电路进入待机状态有赖于过放电状态的检测,进入待机状态后,为了减小功耗应使尽可能多的电路模块停止工作,但如果所有的检测电路都不工作,待机状态将无法退出,为此在设计负载短路检测电路时不引入待机状态控制信号,其目的即为在电池电压升高后使保护电路能及时退出待机状态。图4 给出了待机状态信号产生和撤销的原理图。
图4 中SOD为过放电检测信号,系统处于正常状态时,SOD为高电平,V
M为低电平,因此待机状态控制信号POWERD输出高电平、POWERDB输出低电平。当系统进入过放电状态时,SOD(延时后的信号)变为低电平,MP导通使VM变为高电平,终使POWERD变为低电平、POWERDB变为高电平,它们控制保护电路相应模块停止工作,系统进入待机状态。当对电池进行充电时,由图1可知V
M被强制拉到低电平,使负载短路检测电路的输出信号OUT_LSB变为高电平;此时,不论SOD为何值或非门都将输出低电平,POWERD由此变为高电平,这样,就可实现待机状态的退出。
基准电压电路
为了检测过充电、过放电和放电过流情况,检测比较器需要与基准电压进行比较。由于过充电检测和过放电检测电路之前有采样电路,它们可用相同的基准电压,而过流1 和过流2 需采用不同的基准电压。为了提高芯片的检测,电压基准采用受电源、温度和工艺影响较小的带隙基准源,如图5 所示为具体结构图,其中M
1~M
5 工作于弱反型区,因此该电路具有功耗较小的特点。
电路的工作原理为:由M
1—M
4和R
5组成的自偏置电路产生具有正温度系数的电流,它在电阻R0所产生的压降和具有负温度系数的PN 结压降(D0上的压降)相加,从而输出零温度系数的基准电压VBD;为满足同一电路中输出不同的基准电压源,利用电阻分压将VBD 分成了VBI1及VBI2输出;C0和R6组成启动电路。
由图5 可知, V
GSM2-V
GSM1=I
M2*R
5。M
3 和M
4 组成电流镜,取相同的宽长比,则I
M1=I
M2。因为M1和M2工作于弱反型区,所以:
式(1)中n为亚阈值因子,UT为热电势。M3和M5组成电流镜,则:
设)R=(R
1+R
2)//(R
3+R
4 ),二极管的正向压降为V
D,可以推导输出电压为:

由(3)—(5)式可知,基准电压的与电阻R
0—R
4 的直接相关,为此这些电阻需要采用调整(trimming)技术。

图4 待机状态实现电路
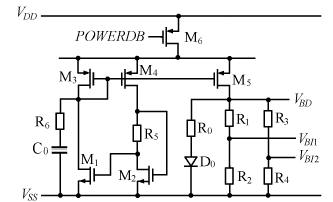
图5 电压基准电路
充电过流检测电路
充电过流的检测归结为检测V
M电压,其临界值为V
CH(约为-1.3V)。如果所用工艺的MOS管阈值电压可以调节,负电压检测电路可用差分结构的比较器实现,其中比较器的一个输入端接地,并且两个差分
对管的阈值电压需要调整。为了使该电路能用常规的CMOS 工艺实现,本文在过零比较器的基础上引入升压电路,如图6(a)所示当V
M》V
CHA时,升压电路使V
N>0 。升压部分具体实现如图6(b)所示。
PMOS管M1和NMOS管M2的栅极都接地。当M1的栅源电压小于它的阈值电压时,M2截止,而M1始终导通,A1比较器的反相输入信号VN电位因为大于同相输入端的电位,而使输出OUT_CDCB为低电平。随着输入信号V
M电位向负方向的增大,M2逐渐导通,使得V
N 端电位变负,OUT_CDCB由此变为高电平。图6中V
N=0时的输入电压即为检测电压V
CHA,此时M
1和M
2处于饱和状态且下列关系式成立:
(6)式中, u
n和u
p分别为N管和P管的迁移率,V
THN和V
THP分别为N管和P管的阈值电压,COX为氧化层电容。(6)式经整理得:
由(7)式可知,本电路中检测电压|V
CHA|的取值只能大于M
2的阈值电压,改变M1和M2的宽长比可改变检测电压V
CHA。当M
2未导通时,电路消耗的电流较小;当M
2导通时,就会有电源到地的通路,为了减小消耗的电流,一般取M1的宽长比小于1。
电平转换电路及0V 电池充电抑制电路 由于电平转换电路和0V电池充电抑制电路的目的都是为了控制CO端,这两个功能可用一个电路完成,如图7 所示给出了具体实现电路。
电平转换功能主要由M
1—M
4、R
1和R
2组成的电路完成;0V电池充电抑制功能主要由M
5、M
6和R
3完成;M
7—M
10和R
4组成的与非门在电平转换功能和0V 电池充电抑制功能之间进行选择。电阻起限流作用。下面是这两个功能的具体实现过程。
电平转换实现过程
在正常的放电过程中,V
M端电位大于零而接近于零,可近似为V
SS。此时,该电路的输入信号IN_LCB=‘0’,IN_LC=‘1’,显然,CO输出为高电平(VDD)。
在正常的充电过程中,V
M端电位小于零而接近于零,仍可近似为V
SS。当出现过充电或充电过流时,IN_LC=‘0’,IN_LCB=‘1’,VA为VM端电位,VB为VDD电位,VC输出V
DD电位,因此CO与V
M等电位。
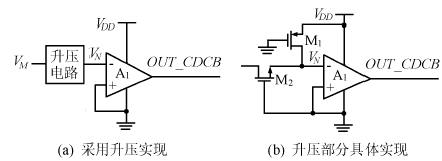
图6 负压检测原理
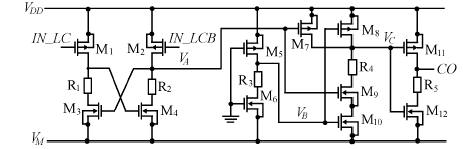
图7 电平转换电路及0V电池充电抑制电路
0V 电池充电抑制实现过程
0V 电池充电抑制功能发生在充电过程中,此时,IN_LCB=‘0’,IN_LC=‘1’,V
A 为高电平。当电池电压V
DD小于或等于1V时,M
5关闭,另外,较小的电池电压使其内阻变小,接近内部短路。在这种情况下充电,充电电流一定很大,导致V
M的电位下降很大,使M
6 导通,VB由低电平转化为高电平,CO端输出电位接近V
M电位。
模拟结果 芯片的所有功能和主要参数均用HSPICE 进行了模拟验证。图8 给出了过充电保护检测和释放波形图,图9 给出了过放电保护检测和释放波形图,其中COMP_OC 为过充电比较器的输出信号,COMP_OD 为过放电比较器的输出信号;芯片的过充电和过放电检测约为30mV,在正常工作时消耗的电流为3.23uA,在待机状态时消耗的电流为0.15uA。
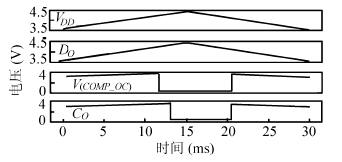
图8 过充电保护检测和释放波形图
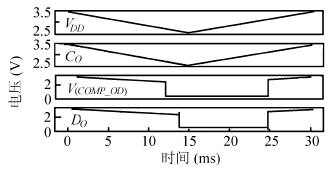
图9 过放电保护检测和释放波形图
总 结 本文设计了一种单节锂离子电池保护芯片,它可用常规的P 阱或双阱CMOS工艺实现。为了提高检测异常情况的,芯片中引入了滤除干扰电路,放电过流采用三级保护机制,电压基准采用带隙基准源;为了降低功耗,采用了如下措施:将模拟电路偏置在弱反型区,引入了待机状态电路;另外,本文用巧妙的电路结构实现了待机状态电路、充电过流检测电路以及0V电池充电抑制电路。经过模拟验证,本文设计的芯片能有效防止锂离子电池在应用中所发生的过充电、过放电和过电流现象,并且具有良好的性能。